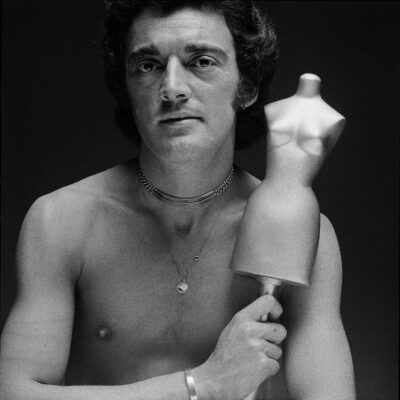
EFHA World 02.04.2024
24.01.2019
fashion historytextile history
Museums around the world have it in their collection, both as cloth and used in dresses, and it is a material much praised for exhibitions and for studies. But what is chintz exactly?
The word ‘chintz’ originally indicated a woodblock printed, painted or stained calico produced in India from 1600 to 1800.
The exotic textile arrived in Europe during the 17th and 18th century on the ships of the East India Companies, all the way from the Coromandel coast in South-East India. It concerned sturdy but shiny cotton fabrics splendidly decorated with floral patterns. It also hardly stained and resisted washing treatments. In English, this marvel was called chintz, a pluralized version of the Hindi word for ‘bright’. Initially these fabrics were used for curtains, furnishing fabrics, and bed hangings and covers. It has been suggested that wearing them as clothes began when these were replaced and given to maidservants, who made them into dresses, and also that they were first worn as linings.
By 1680 chintz had become massively popular; more than a million pieces of chintz were being imported into England,France and The Netherlands per year. As chintz was considered a threat for the national textile industries, French and English citizens were prohibited to either produce, import or even wear it for over 70 years, respectively from 1686 and 1701.
The Dutch East India Company was the main importer of chintz fabrics to Europe during the 17th and 18th century, and this is testified by many engravings. In The Netherlands the sale of both original chintz and reproductions flourished; over the years chintz was used for fashionable and for regional dress. The country was happy to cater to its neighbors, to which the Dutch merchandise and the Indian originals were smuggled. Trying to reproduce Indian chintz, the Dutch entrepreneurs did not choose an easy option. Even though in India most of the designs were painted by hand, printing reproductions in the Low Countries remained time-consuming. Weeks if not months were involved in making the natural dyes, cleaning the fabric (beating it with wooden bats), preparing it with a tannin solution (retrieved from plants), submerging it in various baths, rinsing and drying.
Color dying always happened in the same order: black, red, blue, purple, yellow and green. Some of the colors appeared only when the fabric, hand painted or printed with a type of mordant, was plunged in a dye bath afterwards. Others could be applied to the fabric directly. The bleaching of the white background, which needed to be repeated several times, required a good amount of sun and goat or cow dung. Finishing happened with rice water, in order to make it sturdy; the shiny look was obtained by calendering or by waxing and polishing with a shell.